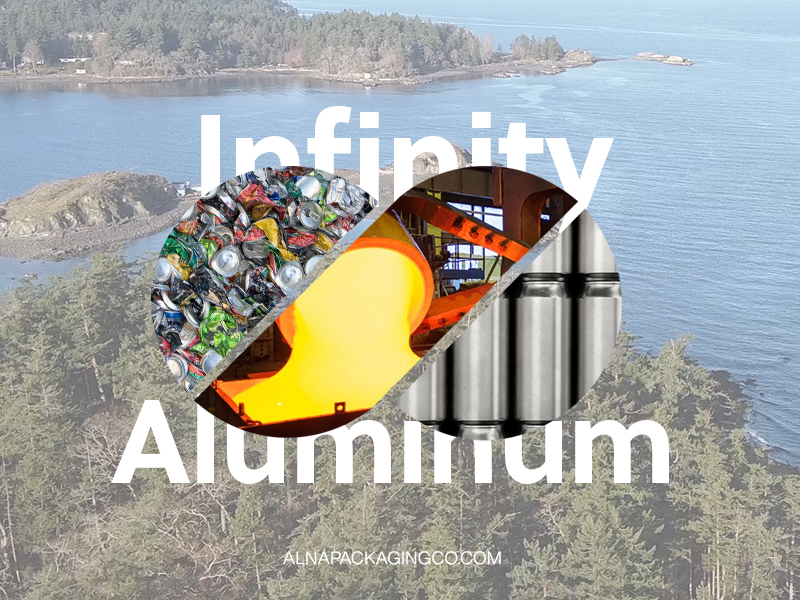
We often herald aluminum as the epitome of recyclability - a material we can use, recycle, and reuse infinitely.
But have you ever wondered how this process unfolds? How are these cans reintroduced into the supply chain? Do manufacturers really benefit from using recycled aluminum? And what about the costs? Is it more or less expensive to produce cans from recycled materials?
At a glance
The Recycling Process
‍Recycling aluminum is a marvel of efficiency. Unlike the laborious process of mining and refining bauxite ore, recycling aluminum involves collecting and re-melting scrap. This streamlined method bypasses the intensive energy demands of the Bayer process, making it environmentally and financially advantageous.
Energy and Cost Efficiency
The real magic of recycling aluminum lies in its energy consumption - it uses a mere 5% of the energy required to produce new aluminum. This translates into significant cost savings, even when accounting for the expenses of collection and recycling. It’s a process that benefits not just the environment, but also the bottom line of manufacturers.
Industry Adoption and Benefits
In the United States, recycled aluminum constitutes about 36% of all aluminum production, indicating the widespread adoption of this sustainable practice. This choice isn't just eco-conscious — it's a strategic investment. Recycled aluminum offers a win-win situation, marrying economic sensibility with environmental responsibility.
The infinite recyclability of aluminum isn't just a neat fact; it's a cornerstone of sustainable manufacturing and a forward-looking investment in our planet's future. As we continue to embrace recycling, aluminum stands out as a material that truly embodies the principles of sustainability and efficiency.